In the ever-evolving landscape of industrial automation and electric motor development, precision remains the cornerstone of innovation. Whether it’s for automotive applications, renewable energy systems, or advanced robotics, the need to accurately measure, control, and optimize motor performance has never been more critical. Appliance motor torque analysis is where hysteresis brakes, hysteresis dynamometers, hysteresis clutches, and integrated motor test systems come into play. These technologies form the backbone of modern motor testing, enabling engineers to push boundaries while maintaining reliability.
UNDERSTANDING THE CORE COMPONENTS
At the heart of any robust motor testing setup lies the hysteresis brake. Unlike traditional mechanical brakes, hysteresis brakes operate without physical contact, relying on magnetic fields to generate torque. This non-contact mechanism eliminates wear and tear, ensuring consistent performance over extended periods. Hysteresis brakes are ideal for applications requiring smooth torque control, such as testing low-inertia motors or simulating dynamic load conditions. Their ability to provide precise, repeatable results makes them indispensable in research labs and production lines alike.
Complementing hysteresis brakes are hysteresis dynamometers, which take testing capabilities a step further. These devices measure torque, speed, and power output with exceptional accuracy. By leveraging the same electromagnetic principles as hysteresis brakes, dynamometers can simulate real-world operating conditions—from sudden load changes to continuous high-speed runs. This allows engineers to validate motor designs under scenarios that closely mimic actual usage, reducing the risk of field failures.
For applications requiring controlled power transmission, hysteresis clutches offer a unique advantage. These clutches use magnetic hysteresis to transfer torque without mechanical linkage, enabling seamless engagement and disengagement. In motor testing setups, hysteresis clutches are often used to isolate components during specific phases of evaluation, such as testing a motor’s response to variable loads or validating regenerative braking systems in electric vehicles.
THE ROLE OF MOTOR DYNAMOMETERS
While hysteresis-based systems excel in precision, motor dynamometers provide a broader framework for comprehensive testing. A motor dynamometer integrates load simulation, data acquisition, and control systems into a single platform. This versatility makes it suitable for testing everything from small DC motors to high-power industrial drives.
Modern motor dynamometers are equipped with adaptive algorithms that can replicate complex load profiles, such as those encountered in hybrid vehicle drivetrains or wind turbine generators. By combining hysteresis technology with advanced software, these systems deliver unparalleled insights into efficiency, thermal behavior, and durability. For instance, automotive manufacturers rely on motor dynamometers to certify compliance with global efficiency standards, ensuring products meet stringent regulatory requirements.
INTEGRATED MOTOR TEST SYSTEMS: WHERE INNOVATION MEETS PRACTICALITY
A motor test system is more than the sum of its parts—it’s a harmonized ecosystem designed to streamline workflows and maximize productivity. Leading-edge systems integrate hysteresis components, dynamometers, and customizable software interfaces to create turnkey solutions. These systems are scalable, allowing users to test single motors in R\u0026D environments or automate high-volume production testing with minimal reconfiguration.
One notable application is in the aerospace industry, where motor test systems validate actuators used in flight control systems. Engineers can simulate altitude-induced temperature fluctuations, vibration profiles, and emergency load scenarios to ensure components perform flawlessly under extreme conditions. Similarly, in the renewable energy sector, test systems help optimize the efficiency of wind turbine pitch drives and solar tracking motors, directly contributing to energy output and ROI.
ADVANTAGES OF HYSTERESIS TECHNOLOGY IN MODERN TESTING
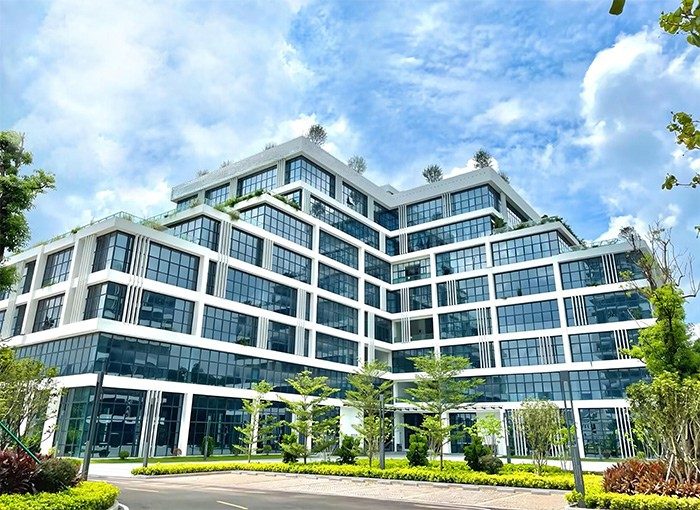
The shift toward hysteresis-based solutions is driven by several key advantages:
1. Durability: With no physical contact between components, hysteresis devices experience minimal wear, reducing maintenance costs and downtime.
2. Precision: Electromagnetic control allows for micro-adjustments in torque and load, critical for testing high-performance motors.
3. Versatility: Hysteresis systems can handle a wide range of speeds and loads, making them suitable for diverse industries.
4. Energy Efficiency: By recovering energy during testing cycles—such as regenerative braking simulations—these systems lower operational costs and environmental impact.
REAL-WORLD APPLICATIONS AND CASE STUDIES
Consider the case of an electric vehicle (EV) manufacturer aiming to extend battery life. Using a hysteresis dynamometer, engineers simulate thousands of acceleration-deceleration cycles to analyze motor efficiency and heat dissipation. The data collected helps refine cooling systems and software algorithms, ultimately increasing the vehicle’s range by 12%.
In another example, a robotics company developing surgical assist devices employs a hysteresis clutch to test precise torque control in micro-motors. The clutch’s ability to apply sub-Newton-meter loads ensures the motors can perform delicate tasks, such as suturing or tissue manipulation, with sub-millimeter accuracy.
NAVIGATING THE FUTURE OF MOTOR TESTING
As industries embrace electrification and IoT-driven automation, the demand for smarter, faster, and more adaptable testing solutions will grow. Emerging trends include the integration of AI for predictive maintenance analysis and the use of digital twins to simulate entire motor systems in virtual environments. Hysteresis-based components will continue to play a pivotal role in these advancements, providing the precision required to validate next-generation technologies.
For businesses investing in motor test equipment, the choice of partner is crucial. Leading providers offer not only cutting-edge hardware but also comprehensive support—from system calibration to regulatory compliance guidance. By selecting a supplier with expertise in hysteresis technology and motor dynamometry, companies can future-proof their testing infrastructure and stay ahead in a competitive market.
CONCLUSION
From hysteresis brakes that deliver frictionless control to motor test systems that replicate real-world stresses, these technologies are redefining what’s possible in motor development. As industries strive for higher efficiency, reliability, and sustainability, the tools used to test and validate motors must evolve in tandem. By embracing advanced hysteresis-based solutions, engineers can unlock new levels of performance, ensuring their products meet the demands of tomorrow’s challenges—today.
Whether you’re designing the next breakthrough in electric mobility or refining industrial automation processes, the right testing equipment isn’t just an investment—it’s a catalyst for innovation.